The Industrial Internet of Things (IIoT) is the grittier end of the Internet of Things (IoT) revolution that is sweeping the manufacturing sector. IIoT alone is estimated to deliver 10-25% productivity improvements, but when combined with analytics, automation, lean approaches, and artificial intelligence (AI) , as recommended by Industry 4.0, the opportunity is many times greater.
I speak from experience. As the IT leader at a group of industrial companies, I had the honor of leading an Industry 4.0-driven IT strategy and operational intelligence initiative that delivered multi-million-dollar results.
Why should your CEO or COO care about Industry 4.0?
Ask your CEO: Would you like increased capacity with minimal capital investment?
Ask your COO: Would you like improved productivity, quality and reduced downtime?
I think I can guess the replies you will receive. Well, these are the opportunities presented by Industry 4.0.
The majority of Industry 4.0 does not require large investments. It does need a proper strategy, time from key people in the operation, and a mindset change to use data to analyze situations and make decisions.
The bottom line: IIoT is a great enabling technology, but when you take an Industry 4.0, end-to-end strategic view, the opportunities are considerably greater.
What is Industry 4.0?
The term Industry 4.0 was first used in Germany in 2011 and covers these key areas:
- Productivity – process efficiencies, better asset utilization
- Asset Reliability – reduced downtime, improved reliability, reduced maintenance costs
- Quality – real-time quality monitoring and correction
- Speed – innovation to production in reduced time
- Sustainability – energy and water management, environmental protection
- Connected Value Chain – connected entire value chain to provide increased flexibility
It aimed to bring together approaches and technology to improve the competitiveness of German industry. Since then, Industry 4.0 has spread across the world and is driving what has been heralded as “the fourth industrial revolution”.
The Four Industrial Revolutions
Where to Start
1. Collect the Data (data is the new oil)
Start with data. But I am not talking about any old business data; this is the specialized area of operational technology. Most production lines consist of a mix of intelligent machines run by programmable logic controllers (PLCs) or Distributed Control Systems (DCSs), and less intelligent equipment such as conveyor belts, tanks, pumps, and so on. By collecting data from all of this equipment through a mix of networked machines, traditional wired sensors and wireless IIoT sensors, you build up a clearer understanding of what is happening in real-time.
Related post: The Industrial Internet of Things – Where the Rubber Meets the Road |
This data might include the number of products made per second, the speed of a conveyor belt, the temperature of an oven, the volume of water consumed per minute, the amount of power consumed by a piece of equipment, or simply whether a machine is on or off.
When this approach is expanded to all machines, devices and people, we build a powerful picture of that production line.
2. Secure the data, give it context, analyze it to find the true value
So now your machinery is generating millions of tiny readings per second, normally referred to as “time-series data”. What do you do with it? You need to store and analyze that data over years of performance. And no, this type of data does not play well in a SQL database! Specialized resources such as a data historian are needed to capture and store this data.
If you then combine this data with contextual information, such as which product is being run, the quality of the raw materials, or even the temperature outside, it gives you the ability to better analyze and understand the performance of the production line.
Using specialized tools for analyzing time-series data allows plant engineers to examine the performance over months or years of production and start to understand what has changed.
3. Expand data collection
If you then expand the collection of data to all production lines and all plants, you will start to build a powerful ability to compare and contrast performance across machines, across lines and across plants. For example:
- Why is the same machine on two different production lines performing differently?
- Why is there a higher level of downtime on the first shift vs the third shift?
- Why is the quality decreasing on certain days?
- Why are we using more water or energy than expected?
4. Leverage for full value
This critical information can then be utilized to drive operational intelligence and approaches such as Lean, Six Sigma, Condition Based or Predictive Maintenance. It allows you to empower the engineers and operators to become true digital workers. It also forms the foundations for other game changers such as increased automation and robotics, all of which can ultimately increase productivity and quality while reducing downtime.
5. Take it to the next level – cyber physical systems
Taking this approach to the next level, in what is often referred to as the ultimate goal of Industry 4.0, are cyber physical systems. This is the coming together of the physical and digital worlds.
- Augmented Reality – using a suitable device, such as a head-up display mounted on a safety helmet, you can overlay the equipment being viewed with key operational data in real-time. This enables the operator or maintenance worker to see a fuller picture of what is happening, access related information, and check specifications without leaving the line. All of this saves time, increases productivity, and ultimately improves the bottom line.
- Digital Twin – use the same information to build a digital model of the production line, which allows you to simulate your operation and understand how it will react to changing conditions, improvements, or new products. It provides an understanding of what is happening now on your production line and predicts what will happen in the future. This is essential to overall manufacturing productivity, reducing downtime, improving quality and business profitability. It allows you to avoid issues and reduce time-to-market for new products.
These are just two examples, but they provide a vision for what the future holds in manufacturing. The reality is that the technology for this is available right now and is becoming increasingly popular.
Industry 4.0 + Industrial Internet = Competitive Advantage
The combination of the right approaches, real-time production information plus technologies such as IIoT helps us build what is often referred to as “smart factories” or “digital factories”.
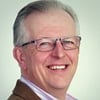
Written by Martin Davis
Martin Davis is a results driven technology and business leader with extensive experience across the consumer goods, frozen/fresh food manufacturing, transportation and automotive industries, delivering value globally in large Fortune 500 corporations and privately held companies. He is currently Managing Partner at DUNELM Associates Ltd, focusing on CIO services, IT strategy, and helping companies drive results through Industry 4.0.